We are committed to satisfy applicable requirements and to provide defect free injection moulded plastic components to our valued customers and meet the price, service, quality and delivery as per their requirement. This is achieved through continual improvement in all areas of our operations and quality management systems.
We are an IATF certified company. We have properly defined Quality Management Systems in place. Additionally, we have a continuous improvement culture in all our operations.
Mulay Polymers Pvt. Ltd - IATF 16949:2016
Mulay Polymers Pvt. Ltd - ISO 9001:2015
We manufacture many performance related products like engine components, gear system components, brake system components and steering column components. The performance of the vehicle depends on the accuracy of these components. So we have prepared special checking aids for checking part runout of components like various fans used in petrol engines. We also use checking and cooling fixtures to maintain the precision of such critical components. The packing also plays a crucial role to maintain part quality and to avoid warpage. So we take special care for such critical components from moulding stage to the customer assembly line.
Crafting Automotive Excellence: Commitment, Precision, and Aesthetic Finesse in Injection-Molded Components
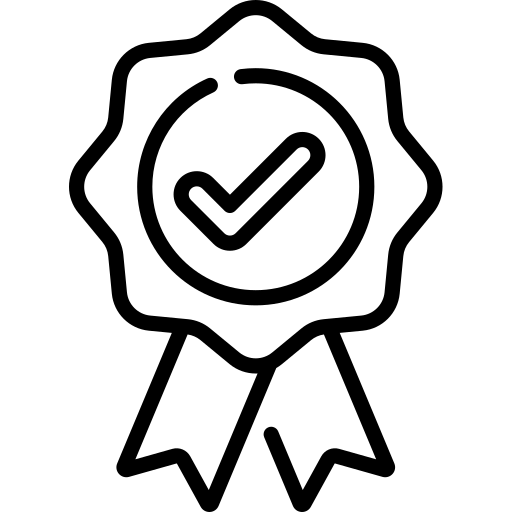
Quality Commitment
Continuous Improvement Culture
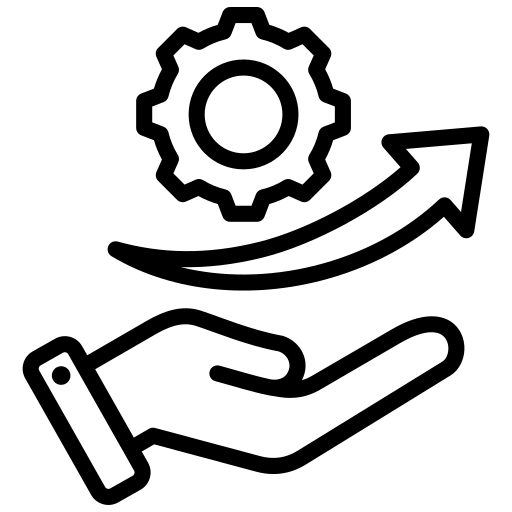
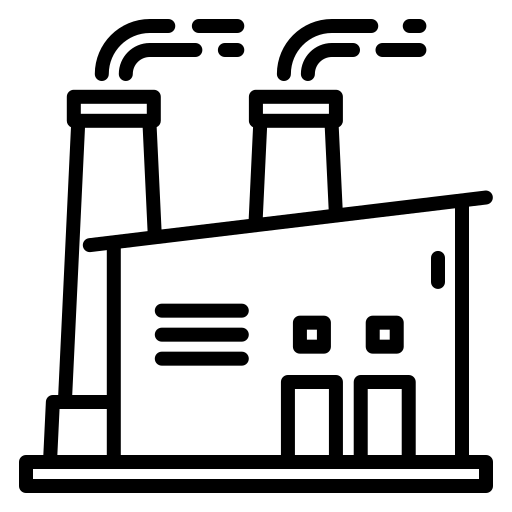
Precision in Manufacturing
Aesthetic Considerations
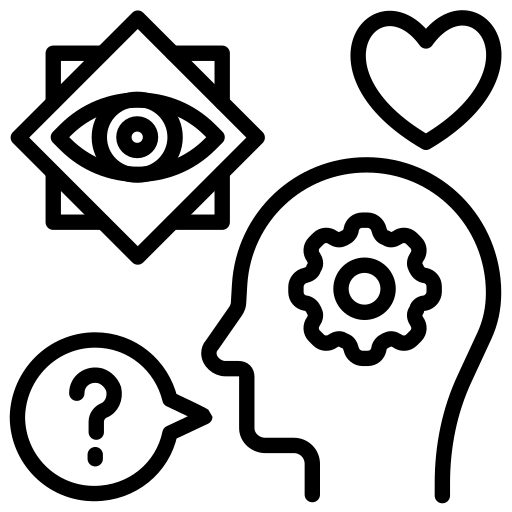
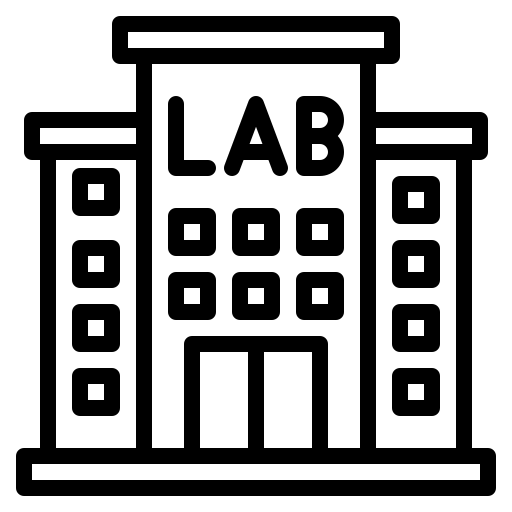
RM Testing Lab
Focus on Finish and Fitment
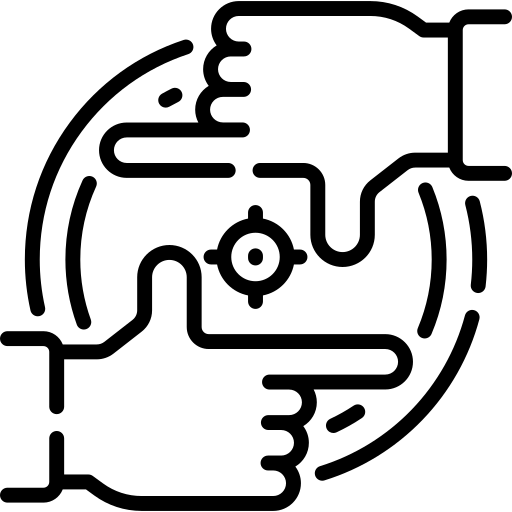
Components’ colour of aesthetic parts is very important as there is a colour scheme defined by the customer while designing the automobile to make the vehicle attractive. So maintaining the same shade of the colour in every part is crucial. We have defined proper processes and inspection systems to make sure that each and every part of every lot adheres to this standard.
We also have an RM testing lab wherein we have equipments like MFI tester, muffle furnace and density meter.
Any product's 1st impression comes from exterior components. So their finish, aesthetic look, and fitment are important. There is a chance that the colours of external components of vehicles might get faded due to UV rays in the sunlight. To avoid this we add UV stabilizer to RM. The part should qualify customer recommended UV tests. We are careful in making sure that the part adheres to the required quality standards. We supply parts having glossy finish which get painted at the customer end.
When the customer goes into the showroom to see the vehicle and sits in the driving seat for the first time, his first impression depends upon the interior of the vehicle. So the components’ colour, finish and fitting become very critical. To make sure that the components perfectly fit on the vehicle during the assembly, we make and use cooling fixtures, checking fixtures and relation gauges.